Understanding Safety Stock: How It Prevents Stockouts [2024]
Master the essentials of safety stock: learn its importance, calculation, and how it ensures smooth operations and customer satisfaction.
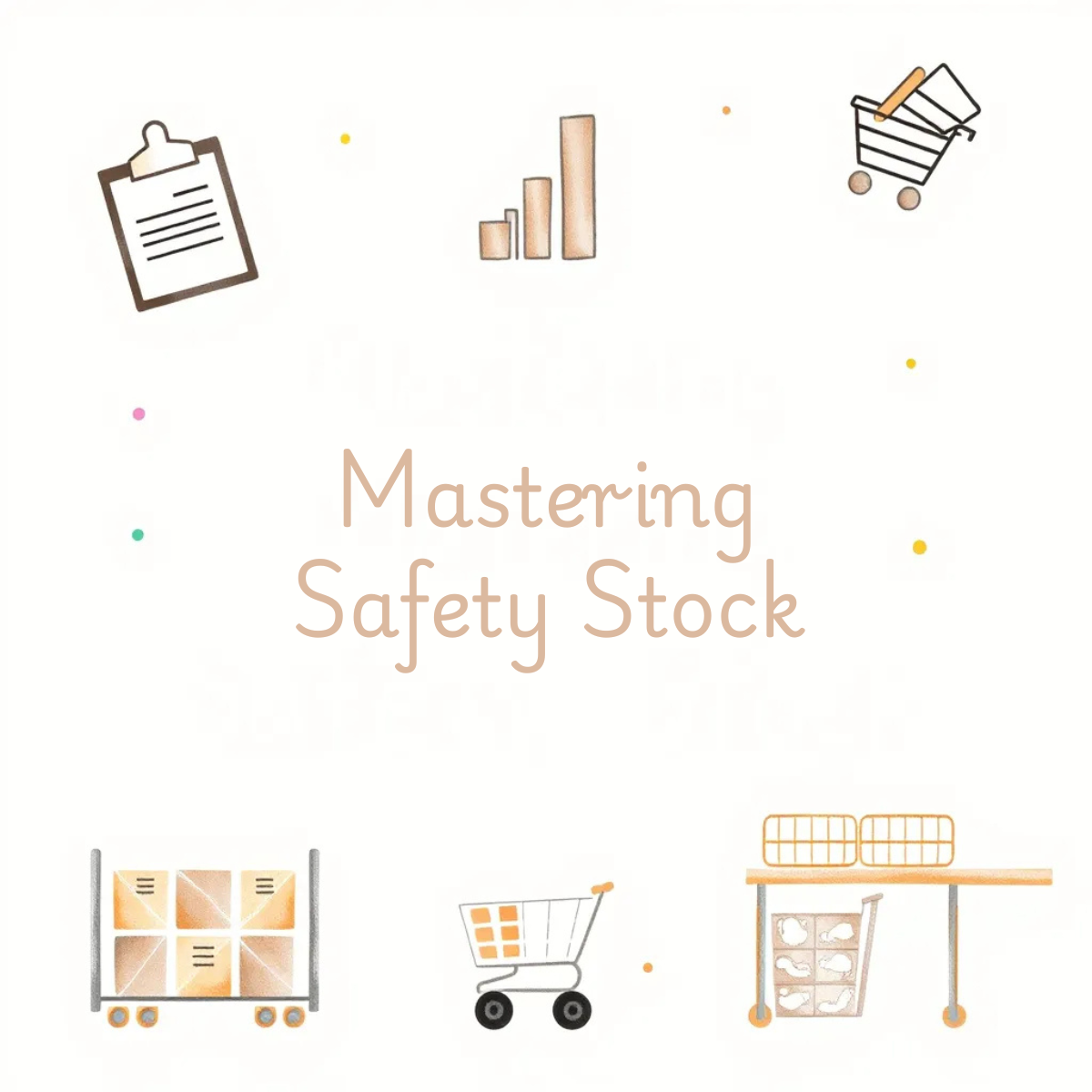
Let’s face it, in today’s fast-paced business environment, maintaining optimal inventory levels is crucial for success. One of the key concepts in inventory management is safety stock. We will now explore further what safety stock is, its importance, how to calculate it, and how it can help prevent stockouts, ensuring that your business runs smoothly.
Table of Contents
- What is Safety Stock?
- Importance of Safety Stock
- Safety Stock Formula
- How to Calculate Safety Stock
- Factors Influencing Safety Stock Levels
- When is Safety Stock Needed?
- Summary
What is Safety Stock?
Safety Stock Definition
Safety stock refers to extra inventory a business may hold to avoid the risk of stockouts caused by uncertainties in supply and demand. It basically acts as a buffer against unexpected fluctuations, ensuring that customers’ demands can still be met.
Purpose of Safety Stock
The main purpose of safety stock is to protect against variability in demand and lead times. For example, if a sudden spike in customer orders occurs or if a supplier delays delivery, safety stock allows businesses to fulfill orders without interruption.
Importance of Safety Stock
Mitigating Risks
In businesses, there are many risks involved, from the initial investments to the many critical decisions that may need to be made. Safety stock plays a vital role in one of the risks involved. It helps businesses to prepare for unexpected events like:
- Demand spikes: Seasonal trends or promotions can lead to increased sales e.g. Christmas, Black Friday, 11.11 promotion etc.
- Supply chain disruptions: Delays from suppliers due to natural disasters or logistical issues.
Business Continuity
By maintaining sufficient safety stock, companies can ensure smooth operations even during challenging times. The importance of business continuity can sometimes be overlooked. When everything is working smoothly, no one bats an eye. However, when disaster occurs, every mistake is scrutinized extensively. Thus, having safety stock allows continuity in fulfilling customer orders, hence, enhancing customer satisfaction and loyalty.
Example
To present the idea in a simple example, consider a retail company that sells seasonal products. By analyzing past sales data from previous years, they determine their average sales during peak season and maintain safety stock accordingly. When demand unexpectedly surges, they can rely on their safety stock to meet customer needs without losing any sales.
Safety Stock Formula
Basic Formula Overview
The calculation of safety stock involves a formula that considers variability in demand and lead time:
Safety Stock = Z × σ × √L
Where:
- Z is the service level factor (reflecting the desired probability of not running out of stock).
- σ is the standard deviation of demand.
- L is the lead time (the time it takes for inventory to arrive after an order is placed).
What does ‘Z’ Represent?
The ‘Z’ value represents the desired service level. This value can be obtained from a standard normal distribution table, which is used in safety stock calculations to represent desired service level. For example, a Z value of 1.65 corresponds to a 95% service level, meaning there’s only a 5% chance of running out of stock during the lead time.
Here are some common service levels and their Z-scores:
How to Calculate Safety Stock
Step-by-Step Calculation Guide
Do not worry; calculating safety stock can be straightforward if you follow these steps:
- Determine your average demand: Analyze historical sales data.
- How to find it:
– Gather historical sales data.
– Calculate the average demand for a given period (e.g., daily, weekly, monthly)
– Formula:
Average Demand = Total Demand Over Period / Number of Periods
Example: Your daily demands are as follows:
- Day 1: 90 units
- Day 2: 100 units
- Day 3: 110 units
- Day 4: 80 units
- Day 5: 120 units
(90+100+110+80+120) / 5 = 100 units per day.
- Calculate the standard deviation of demand: This reflects variability in your sales.
- How to find it:
– Use historical demand data.
– Calculate the variance of the data:
Variance = ∑(Demand - Average Demand)² / (n-1)
(where n is the number of data points)
– Take the square root of the variance to get the standard deviation: σ = √Variance
– Tools: Use Excel, Google Sheets, or statistical software to calculate this easily.
– Example:
Each day’s demand deviation from the average:
- Day 1: 90 − 100 = −10
- Day 2: 100 − 100 = 0
- Day 3: 110 − 100 = 10
- Day 4: 80 − 100 = −20
- Day 5: 120 − 100 = 20
Square these deviations to make them positive:
- Day 1: (-10)² = 100
- Day 2: 0² = 0
- Day 3: 10² = 100
- Day 4: (-20)² = 400
- Day 5: 20² = 400
Add up all the squared deviations:
100 + 0 + 100 + 400 + 400 = 1000
Calculate the variance using the earlier formula:
Variance = ∑(Demand - Average Demand)² / (n-1)
= 1000 / 4
Standard deviation of demand = √250 = 15.81 units.
- Identify your lead time: Understand how long it takes for your suppliers to deliver.
- How to find it:
– Check supplier contracts or agreements.
– Use historical data on supplier delivery times.
– Consider any delays or variations.
– Example: If it takes 10 days on average to receive shipments, then L = 10 days.
- Choose your desired service level: Decide on the Z-value based on how confident you want to be about not running out of stock.
- How to find it:
– Decide your service level (e.g., 90%, 95%, or 99%).
– Refer to Z-score table to find the corresponding Z-value.
– For example:
90% Service Level → Z = 1.28
95% Service Level → Z = 1.65
99% Service Level → Z = 2.33
Safety Stock Calculation Example
Referring to the earlier example, if your average daily demand is 100 units, the standard deviation is 15.81 units, and your lead time is 10 days with a Z value of 1.65 for a 95% service level:
Safety Stock = Z × σ × √L Safety Stock = 1.65 × 15.81 × √10 = 82.49
This means you should hold approximately 83 units as safety stock.
Factors Influencing Safety Stock Levels
Demand Variability
Fluctuations in customer demand can significantly impact how much safety stock you need. The best way to analyze this from a technical aspect is to look at historical data and trends to anticipate changes in demand accurately.
Lead Time Variability
Variability in supplier lead times can also affect safety stock calculations. If suppliers frequently change delivery times, it’s crucial to adjust safety stock levels accordingly.
Desired Service Level
There is no hard and fast rule when it comes to service level because it may differ for different businesses. Each business would need to determine its target service level based on customer expectations and market conditions. Higher service levels require more safety stock but can improve customer satisfaction.
When is Safety Stock Needed?
Identifying Triggers for Safety Stock Use
There are specific scenarios where safety stock becomes critical:
- During peak seasons or promotional events
- When launching new products
- In response to sudden changes in market conditions or consumer behavior
What is Reduced by Safety Stock?
When utilizing the concept of safety stock in your business, you reduce:
- The risk of lost sales due to out-of-stock situations
- The potential for dissatisfied customers
- The financial impact associated with emergency orders or expedited shipping costs
Summary
Understanding and managing safety stock is essential for any business aiming to prevent stockouts and maintain smooth operations. Although these calculations may seem daunting, it is important to consider the optimal safety stock needed based on demand variability, lead times, and desired service levels, as this ensures a company’s preparedness for unforeseen circumstances. As an alternative to such manual calculations, OneCart offers automated tracking of orders and inventory. With programmed calculations tailored to your business operations, you can anticipate stockouts and take action immediately.
Want to optimize your operations and prevent stockouts? Try OneCart today for a free trial!